THE EVOLUTION OF PLATINUM JEWELLERY ALLOYS: FROM THE 1920s TO THE 2020s
a speech by Christopher W Corti
Abstract
Platinum has only been known to Europe since the 16th century. This was impure platinum which is found as grains of native metal in alluvial deposits, often associated with native gold. Such grains are mainly platinum alloyed with the other 5 platinum group metals and were exploited by pre-Colombian Indians of Ecuador and Colombia in NW South America.
In more recent times, the popular use of platinum in jewellery dates from the early 20th century, often as a basis for diamond (and other precious gemstone) jewellery. Its use in jewellery was restricted in the Second World War as it was considered a strategic industrial metal with limited availability. Thus, early jewellery alloys tended to be based on the existing industrial alloys and comparatively little development of specific jewellery alloys was carried out. Its acceptance as a hallmarkable jewellery metal came much later in 1975 when, with a wider availability of the metal, platinum was promoted as a high value jewellery metal and platinum jewellery started to grow in popularity, mainly at 950 and 900 fineness qualities. Since that time there has been alloy development specifically for jewellery application and tailored to the requirements of different manufacturing technologies.
This presentation reviews the evolution of platinum alloys over the last century against the challenges – physical and metallurgical – presented in developing improved alloys for jewellery application.
INTRODUCTION
Platinum has only been known to Europe since the 16th century with rumours of the existence of a white metal, platina, in central and south America that cannot be melted1. This was impure platinum which is found as grains of native metal in alluvial deposits, often associated with native gold. Such grains are mainly platinum alloyed with the other 5 platinum group metals (PGMs – palladium, rhodium, ruthenium, osmium and iridium) – and were exploited by pre-Colombian Indians of Ecuador and Colombia in NW South America. Analysis of ancient trinkets indicates that iron and copper were also present as impurities1.
JEWELLERY ALLOYS: 1920s to 1999
In more recent times, the popular use of platinum in jewellery dates from the late 19th– early 20th century, often as a basis for diamond (and other precious gems) jewellery. Smith, in his book published in 19332, notes its use in jewellery at 99.5% fineness with small additions of alloying metals to harden it, including Ir, Rh, Ru, Au, Ag and Cu. He also notes that the platinum standard (in the UK) is 950 fineness and is finding general acceptance. The term ‘platinum’ is deemed to include iridium. He further notes that much of the platinum in use in jewellery is alloyed with copper to improve hardness and colour. The use of platinum in jewellery was restricted in the Second World War as it was considered a strategic industrial metal with limited availability, which led to the development of white gold alloys as an alternative for jewellery. Thus, early jewellery alloys tended to be based on the existing industrial alloys and comparatively little development of specific jewellery alloys was carried out. These tended to be 90-95% platinum alloyed with other PGMs, usually iridium. These alloys have high melting temperatures, making manufacturing of jewellery, particularly investment (lost wax) casting, difficult and challenging for the jeweller used to gold and silver.
A further issue had been the lack of accurate analysis techniques. All this meant that its acceptance as a hallmarkable jewellery metal in the UK came much later in 19753. From this time, with its now much wider availability, platinum was promoted by the platinum producers as a rare, high value jewellery metal and platinum jewellery grew in popularity, mainly at 950 and 900 fineness qualities, in Japan, Europe and the USA, although some growth in demand began earlier in Japan in the 1960s for historical reasons linked to the ban on the import of gold until 1973. This marketing and growth led to some alloy development such as the platinum-cobalt alloy for investment casting4 and the use of gallium additions to produce heat treatable alloys with higher strength and hardness5 as Normandeau has reported6. For example, one European platinum producer lists only 4 alloys for jewellery application in their catalogue dating to the late 1980s, all at 950 fineness, namely platinum – copper, platinum – cobalt, platinum -ruthenium and platinum-gallium-indium. The copper alloy is listed as a general purpose alloy and the cobalt alloy is listed as suitable for investment casting. Another European producer lists only 3 alloys at 950 fineness: Pt-5Cu, Pt-5Co/Ni and Pt-5Ru.
Huckle of Johnson Matthey reported on the development of platinum alloys to overcome production problems at the 1996 Santa Fe Symposium7. He noted that platinum and its alloys had some different characteristics compared to gold and silver, notably weight, hardness and thermal conductivity and that its alloys have a high density, as well as high melting points. Its high surface resistance leads to clogging (galling) and high wear of saw blades, files and machine tools. He notes that, in Japan, Pt-Pd alloys are in common use, particularly Pt-10%Pd, whereas in Europe Pt-5% Cu is preferred but that it is not a good casting alloy whereas for casting application Pt-5%Co is finding success. In the USA, he notes Pt-10%Ir is commonly in use as an all-purpose alloy and that Pt-5%Ru is used where a hard, good machining alloy is needed. He also notes Pt-5% Co is finding growing use for casting applications in the USA.
Maerz (Platinum Guild International) also reviewed platinum jewellery alloys at the 1999 Santa Fe Symposium8 and this built on the information provided by Huckle. It sums up the alloys widely available and their application in jewellery at that time with some comment on the new alloys being introduced, Table2.
In this context, Maerz and Huckle noted that it is important to recognise the different marking standards of various countries at that time. Maerz noted that European countries generally allowed only 950 fineness alloys, with some allowing no negative tolerance (Austria, Ireland, Sweden, Norway, Finland, United Kingdom and Switzerland), some allowing a small negative tolerance (Denmark, Portugal and Italy) and others allowing iridium content to be counted as platinum within the 950 standard (Belgium, France, Italy, Greece, Netherlands and Spain). In Germany, he noted that several fineness standards and alloys were allowed, Table 1.
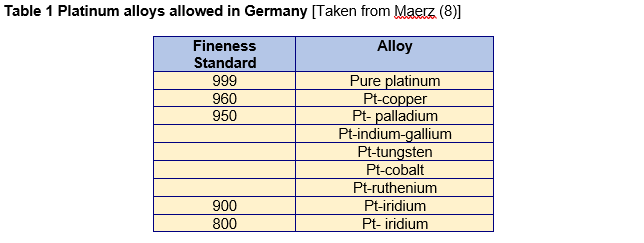
In the USA, he noted that the standard for jewellery to be marked as platinum was 950 fineness but that the minimum amount of platinum allowed was 500 parts per thousand with the rest of the alloy comprising 950 parts per thousand total platinum group metals (PGMs) with a zero tolerance. He also notes that 950,900 and 850 fineness standards are allowed in Japan.
With regard to actual alloy compositions, he notes that each alloy is made for specific manufacturing functions. Some alloys are preferred for tubing or machining and others for casting, for example, and there are differences in preference in different countries. Table 2 lists the alloys in common (or growing) usage around the world with their function and countries of major use. He also lists separately a number of alloys that are specific to Japan
Maerz’s list did not record the platinum-5% copper alloy (except its use in Japan) which has been mentioned above as an alloy commonly used in Europe. Maerz does note that, in the USA, the most common alloys in use are 950 platinum with 5% cobalt or ruthenium and 900 platinum – 10% iridium alloy. However, in an updated later version of this paper9, the Pt-5Cu alloy is included.
In his book published in 1984, Savitskii10 notes only two 950 fineness alloys are in use in the old USSR – Pt-5 Ir in Russia and Pt-4.5 Pd – 0.5 Ir in East Germany (GDR).
TECHNICAL ASPECTS OF ALLOYS: 1920s to 1999
From the list of alloys summarised in Table 2, it is evident that at 950 and 900 fineness qualities, there is a broad range of alloys available to the jeweller, each suited to various manufacturing techniques. All have a good white colour, although some may benefit from rhodium plating, e.g. Pt-10% Pd alloy, to give a brighter, whiter colour. The main differences lie in their hardness (or strength) and melting ranges.
Battaini has examined the microstructure of several platinum alloys11 and notes many alloys are single phase, as one might expect from examination of their phase diagrams, particularly at 950 and 900 fineness qualities. Some alloy systems, however, show large areas of miscibility gaps at low temperatures, for example Pt-Au and Pt-Cu systems and this raises the possibility of age-hardening alloys by heat treatment. Platinum-5% gold is an example here, Fig 1(a), where an aged hardness of HV300 can be attained, leading to better scratch and wear resistance, but I have not observed its use in as-cast Pt-Au rings12,13, suggesting it is a treatment not in common use. Platinum- cobalt, Fig 1(b), forms an ordered intermetallic compound, Pt3Co, that could also enable some hardening at 950 fineness. The use of gallium also allows age hardening, as is evident from the phase diagram, Fig 2, as well as lowering melting ranges and its use forms the basis of several heat treatable alloys as noted earlier.
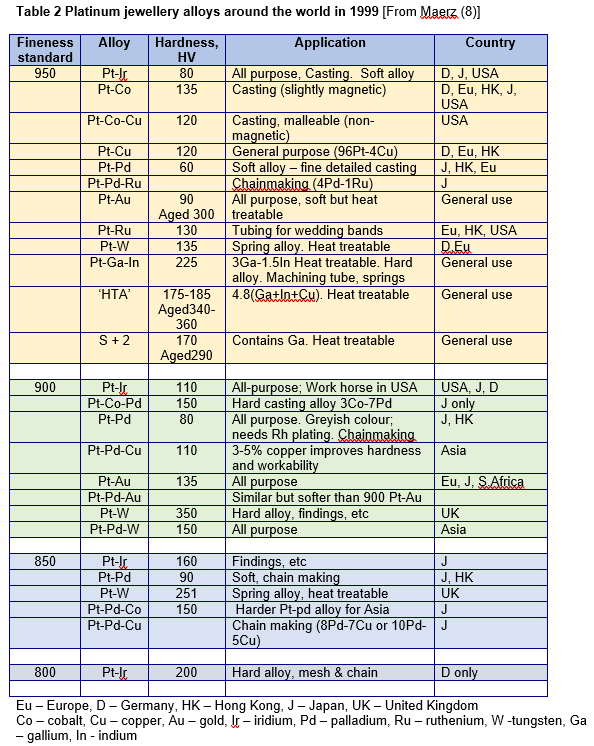
Clearly, some alloys are quite soft (hardness lies in range HV50-100), some have a moderate hardness (HV100-150) and others are quite hard (HV 150 – 350), the higher values usually when in the age-hardened condition. In a recent study by the author of customer complaints12,13, it has been noted that use of soft alloys is a significant factor in platinum jewellery becoming deformed in shape and badly scratched when worn by consumers, particularly in as-cast gem-set rings and wedding bands.
Work around the turn of the 21st century and summarised in recent reviews14,15 has demonstrated that microalloying of pure platinum and its alloys with small additions of calcium and/or rare earth metals such as cerium, samarium and gadolinium, typically up to about 0.3%, can increase hardness substantially but such micro-alloys do not appear to have been commercialised by the jewellery industry, probably because they are not easily cast or recyclable.
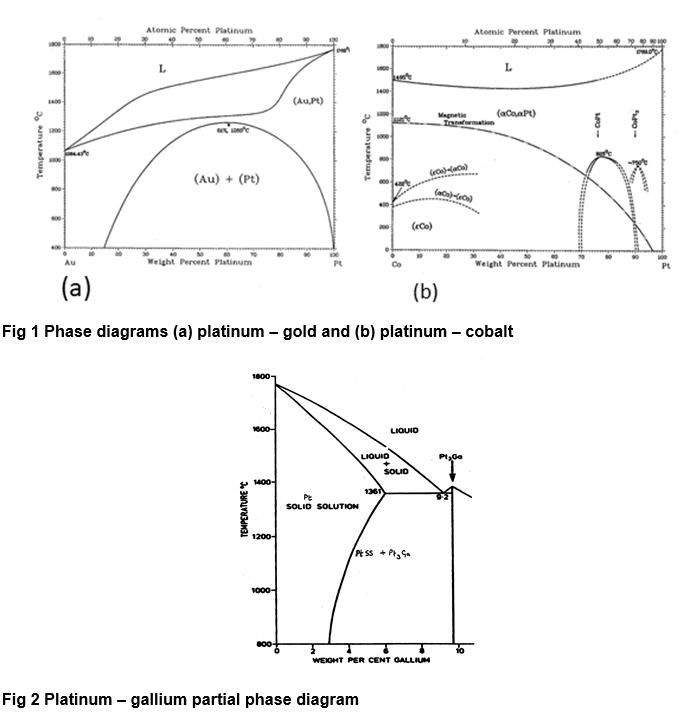
The melting point of pure platinum is 1769°C, considerably higher than gold (1064°C) and silver (961°C). Its alloys tend to have similarly high melting ranges, as shown in Table 3, although the gallium-containing alloys do have a significantly reduced melting range. Thus, melting and casting platinum alloys requires good furnace equipment capable of attaining melt temperatures some 100°C above the liquidus temperature of the alloy for investment casting. Induction melting is preferred. Melting by gas torch is not easy, although a propane or hydrogen-oxygen torch can be used by bench jewellers. However, in general, working of platinum alloys is not a problem, although polishing requires skill and effort to obtain a good quality polish. Machining of platinum also requires skill to obtain a good smooth finish, requiring special tool materials and different tool geometries16, as platinum tends to gall (adhere) on the tool. The low thermal diffusivity of platinum alloys makes welding easier, particularly laser welding18 compared to gold and silver alloys.

The major manufacturing problem has been with investment casting. The high melting and casting temperatures require use of special phosphate bonded investment mould materials19 and the poor melt fluidity requires use of centrifugal casting machines20 to obtain good mould fill rather than the modern gravity machines commonly used for gold and silver. The new generation of tilt casting machines are also suitable. The chief problem with platinum casting is getting defect-free castings7,20,21 and there have been several investigations on the relative merits of different alloys4,22-24, looking particularly at surface quality, form-filling and gas and shrinkage porosity. The general findings from these studies show the Pt-5%Co alloy to be the best of current alloys but still not ideal.
JEWELLERY ALLOYS: 2000 to the Present
There have been several studies to develop improved platinum jewellery alloys in the last two decades. These have focussed on either stronger (harder) alloys or improved investment casting
alloys, although alloys suitable for additive manufacturing (3D printing) technology have also been of interest.
A] Stronger, harder alloys
The resistance of jewellery to abrasion and knocks – wear and scratch resistance – depends to a large extent on the hardness of the alloy. As noted earlier, a study of customer complaints showed platinum rings and wedding bands to be particularly prone to deformation of shape (misshapen) and to heavy wear (scratches and dents) during customer service (i.e. whilst being worn), when made in soft – moderately hard alloys. Hard alloys tend to be difficult to work in manufacture, especially to set gems in mounts, and so it is advantageous if an alloy is relatively soft whilst being manufactured into a piece of jewellery but can be subsequently hardened to improve its durability whilst being worn by the customer. This can be achieved by age hardening of suitable alloys after manufacture, a treatment involving the precipitation of a dense dispersion of fine particles of a second phase within the matrix grains.
For platinum, it has been noted that some current alloys are age-hardenable and alloys containing gallium have been developed specifically for this purpose. The first was the Pt-3% Ga-1.5% In alloy developed by Johnson Matthey5 and others have also followed such as the HTA alloy6 developed by Imperial Smelting and the ‘S’ alloys developed by S Kretchmer and discussed by Maerz8. Weisner, in a paper25 presented in 1999, discusses heat treatable alloys and notes earlier work at Degussa, C Hafner, Johnson Matthey (Pt-Ga-In) and S Kretchmer (Pt-Ga-Pd) to develop heat treatable 950 platinum alloys. He notes that all are ternary alloys, many with melting ranges much lower than the conventional binary alloys, suggesting they all contain gallium and/or indium additions. Such alloys are useful for their spring properties in springs and clasps, for example.
Research26 carried out at Mintek, South Africa in 2005 has examined potential platinum alloy systems with additions of 7% or less to identify suitable binary alloy systems that can be substantially age-hardened. Over 20 alloying metals were studied in the preliminary trials at levels of addition of 2 & 4 % and those showing promise were also studied at the 3% addition level. From this work, alloys with additions of Ti, Zr, Sn, Ga, Ge, Mg, In and V were studied in more depth. From this, along with consideration of other aspects, it was concluded that the best alloy was a Pt-2% Ti alloy which had as cast and annealed hardnesses sufficiently low to be easily worked and formed but with subsequent heat treatment, the hardness value could be increased by about HV90. Interestingly, there are parallels here with the development of 990Gold (Au-1%Ti) alloy27. The Mintek work does not appear to have been further developed into a commercial alloy, possibly because it does not show much advantage over the existing commercial gallium-containing alloys.
More recently, a harder general purpose alloy, TruPlat™, has been introduced to the market in the USA by Hoover & Strong. It is a 950Pt-Ru-Ga alloy that is not age-hardenable. It has a higher work hardening rate compared to 950Pt-Ru, with an annealed hardness of HV180.
B] Improved casting alloys
The motivation here is to develop alloys less prone to casting defects, particularly casting porosity. Use of alloys with lower melting ranges to inhibit mould reaction is desirable too. Work carried out by Fryé at Techform and Klotz and co-workers at FEM 23,24 28-30, 32 on platinum cast in shell and conventional moulds has focussed on which alloys are best in terms of casting porosity formation, form-filling and surface quality and establishing the mechanical properties of cast alloys. The use of computer simulation of the casting process has also assisted in optimising process parameters in casting. Fryé has also shown the benefits of a Hot Isostatic Pressing (HIP) treatment post casting in removing porosity from castings and improving mechanical properties. What is particularly noticeable is the growing number of new platinum casting alloys that feature in these studies. This alloy development started a little earlier in 1997.
In a paper34 presented at the 1997 Platinum Day symposium in New York, Lanam, Pozarnik and Volpe reported on a new investment casting alloy, 950 Pt-Cu-Co, developed at Engelhard, that combines the good properties of Pt-5Co and Pt-5Cu and reduces the issue of magnetism in Pt-Co alloy. It’s as-cast hardness is about HV119, somewhat lower than Pt-5Co. Porosity was still present and it had a tendency to form a surface oxide on heating.
Another alloy development was presented by Normandeau in 200035 in which he reported on a new 950 platinum Hard Casting Alloy (HCA) with an as-cast hardness of HV 160-170, much higher than Pt-5Co alloy. Little detail is given on the composition but the discussion in the paper points to it being a 950Pt-Ga-Ir alloy, since he provides data on the Ga:Ir ratio and it’s effect on hardness.
A further alloy development was presented by Grice & Cart in 200236 where the development of a 950 Pt-Au-X alloy, PlatOro™, is reported as an alternative to Pt-5Co. This has an as-cast hardness of HV125, a little softer than Pt-5Co alloy but is non-magnetic and has lower melting range of 1590° – 1629°C. This does not appear to be the Pt-Au-In alloy examined by Fryé & Klotz30 and Maerz and Laag33, Table 4, since the melting ranges and hardness values are different. Grice has since reported37 that the PlatOro™ alloy is actually a Pt-Au-Cu alloy but is no longer commercially produced.
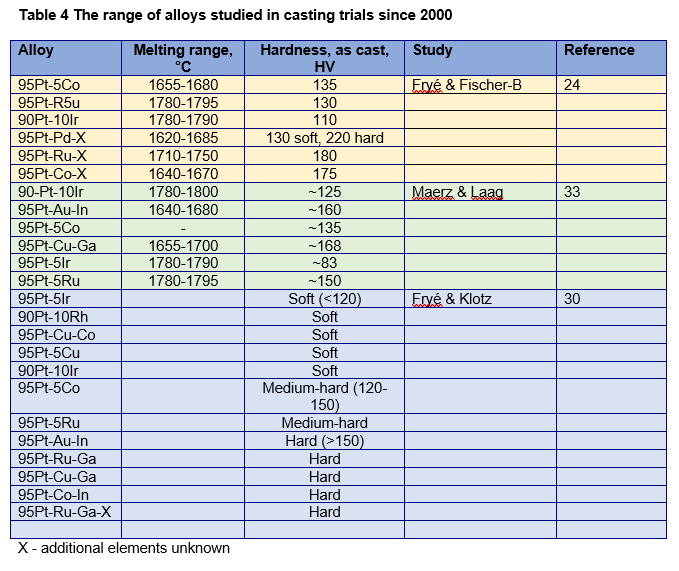
Fryé and Fischer-Buehner in their study reported in 201124 recognised the inadequacies of the existing commercial casting alloys and widened their search to include 3 newer versions that contained undisclosed elements, which they designated as hard alloys (HV175 or greater). These are included in the table of alloys reported in Table 4. The platinum-cobalt- X hard alloy with unknown additions appeared to show some promise. The Pt-Ru-X alloy is now known to be the Pt-Ru-Ga alloy from Hoover & Strong37 and the Pt-Co-X alloy is a Pt-Co-In alloy from Legor38 and is harder and non-magnetic compared to Pt-Co.
In 2014, Klotz et al at FEM utilised computer simulation of casting and thermodynamic calculations to optimise the process parameters of casting Pt-5Ru and Pt-5Co alloys29 and was significant in that ternary alloys of 950 platinum-cobalt-ruthenium alloys were explored. Improved form-filling and surface quality resulted from additions of Co to Pt-Ru alloys, the optimum amount depending on casting technique – centrifugal or tilt casting.
Maerz and Laag33 studied six alloys in their 2016 study, Table 4, which used tilt casting (as opposed to centrifugal casting) in their trials. Two contained gallium or indium and these alloys showed higher as-cast hardness and were rated high in terms of castability. Each alloy had different strengths and weaknesses and the authors concluded that no alloy was perfect but that progress was being made. It is noted that C Hafner patented an alloy, 950 Pt-Au-In in 2013, with the use of Ir or Ru as grain refiners39, which is probably the alloy referred to in Table 4
The largest range of alloys was studied by Fryé and Klotz, Table 4, who also measured mechanical properties and wear resistance of castings30. They warned against use of soft alloys in cast jewellery and noted pronounced micro-segregation in Ga- and In-containing alloys which increased micro shrinkage porosity. Hot isostatic pressing treatment (HIPing) after casting eliminated porosity and restored ductility. They also noted wear was related to hardness, harder alloys wearing less.
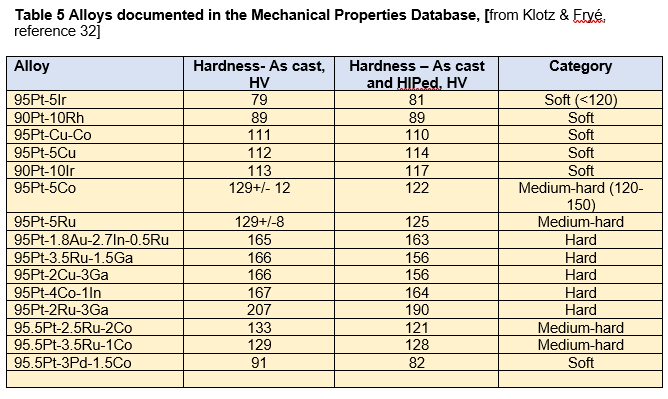
It is clear from the foregoing that no new alloy completely met the desired casting requirements, although a database of mechanical properties of many of the casting alloys was established by Klotz and Fryé for alloys in the as-cast and in the HIPed condition32. This database has data on 13 compositions at 950 fineness and 2 at 900 fineness. As well as the conventional compositions described in Tables 2 and 4, it also includes some newer ternary/quaternary compositions, as shown in Table 5, which only lists the hardness values; perhaps, it also clarifies some of the unknown compositions documented in Table 4.
A more fundamental approach to improved casting alloy design39 has been undertaken recently by Professor Glatzel and his co-workers at the University of Bayreuth and Richemont International. They looked to develop an improved casting alloy of 950 fineness with the following requirements:
- Low casting temperature
- Small melting range
- Microstructure that is homogenous, fine-grained (100 – 150 µm) and with low porosity
- Hardness in range Hv 155-170 for wear resistance and good ductility (>30%)
- Good reflectance with a bright surface
- Alloying elements that are biocompatible and recyclable
Their benchmark alloy was the 95Pt-1.8Cu-2.9Ga which is a recent alloy development (see Tables 4 & 5). Excluding allergenic, radioactive and toxic elements, 25 possible alloying elements were selected and ranked according to a Suitability Index which comprised 4 characteristics: maximum solubility in platinum (Cmax), hardness Index (Hi), melting interval index (Mii) and liquidus temperature change index (Tlci). From these, a first iteration of 5 alloys were selected for testing and following this, a second set of 5 alloys were selected for testing. Casting was performed in a tilt casting machine. These alloys contained up to 5 alloying elements from a list including Al, Au, Cu, Cr, Fe, Ir, Mn, Pd, Rh and V. From these 10 alloys, two in the second iteration were found to be the most promising, Table 6. It is very evident that these compositions are radically different from those listed in Tables 4 and 5. They have a hardness of HV 164 (A2) & 165 (B2) respectively compared to HV 225 for the benchmark Pt-Cu-Ga alloy. It will be interesting to see if these or similar alloys are developed to commercial status and find a niche amongst the current alloys. With the base metal alloying elements including iron and manganese, it is possible there may be tarnishing issues with such alloys, if we compare the experiences in developing alternative white gold compositions.
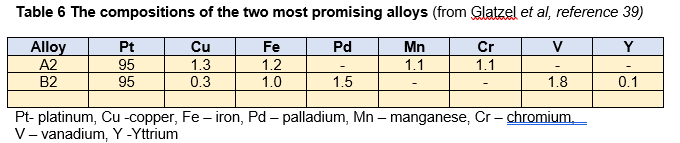
C] Alloys for Additive Manufacturing (3D Printing)
The development of Additive Manufacturing (3D printing) of jewellery has attracted much interest in the industry in recent years and considerable R & D has been carried out on developing machine technology, build techniques and suitable alloys. The technology involves selective laser melting (SLM) of successive layers of alloy powders, and it has become evident that such powders need to be tailored in composition to suit the process. Alloying additions of high vapour pressure metals are not desirable, for example. In the field of carat golds, it is also important to reduce reflectivity and thermal conductivity/diffusivity to better absorb energy and inhibit heat loss through the metal, thus enhancing consolidation of the powders during laser melting. Examples of modifying carat gold alloy compositions have been discussed40. Regarding platinum alloys, these tend to have considerably lower thermal conductivities as has been discussed by Wright in terms of laser welding18 and Zito in terms of 3D printing of jewellery41 Work at Progold Spa on laser selective melting of 950 fineness platinum jewellery has been reported by Zito and his co-workers41-44. In his 2014 paper41, Zito used an unspecified 950 Pt alloy powder whilst in his 2015 paper43, Zito used a 950 platinum alloy powder ‘with alloying additions slightly different from the cobalt-containing alloy used in the preceding work’ but gives no further details other than to say it was not doped with semiconductor elements to reduce thermal conductivity (as was done with the carat gold alloys in his work). In the 2018 paper, in which jewellery made by SLM is compared to the same pieces made by investment casting44, Zito notes the items produced by casting and by SLM were made in the same 950 Pt-Cu-Ga-In alloy but gives no details on actual composition. This is different from the casting alloys discussed in the earlier section, in that it contains indium as well as copper and gallium.
Thus, it appears that there is little need to develop special alloy compositions suited to 3D printing technology; the conventional alloys are acceptable and do not appear to pose any major problems.
D] Other Alloys
To conclude this paper, I note there are other recent alloy developments that appear in the patent and other literature that do not fit into the 3 preceding categories. For example, European Patent applications from Heimerle and Meule45 describe alloys that have optimised processing properties at 950 and lower finenesses based on Pt-W-Cu –(Ru/Rh/Ir) and described as having high hardness and abrasion resistance. The Ru/Rh/Ir additions act as grain refiners.
Another patent from the watchmaker, Omega SA46, concerns 950 platinum alloys that are cobalt- and nickel-free, based on Pt-Ir-Au-Ge- (Ru/Rh/ Pd/Sn/Ga/Re) that have mechanical properties that meet the criteria for watchmaking whilst having the colour and luminosity of Pt-Ir alloys.
CONCLUSIONS
- There has been an evolution of – and growth in – platinum alloy compositions for jewellery application since the 1920s, with a focus on developing alloys suited to the manufacturing technologies in current use. Until the advent of the 21st century, most platinum alloys for jewellery were based on the existing industrial alloys with the platinum -iridium alloys favoured in the early part of the 20th century.
- There is now a wide range of alloys available at 950 and 900 fineness levels with a spectrum of properties. Of note has been the development of heat treatable alloys containing gallium.
- The investment casting of platinum alloys remains a major issue in terms of surface quality and defect formation, particularly gas and shrinkage porosity. The use of hot isostatic pressing post casting removes porosity and improves mechanical properties. As yet, there is no ideal casting alloy to replace the universally accepted Pt-5Co alloy..
- There has been a major evolution in platinum alloys, particularly for investment (lost wax) casting application, in the last two decades (21st century). A recent substantial, structured alloy development approach has produced some significantly different casting alloys containing up to 5 alloying metals It remains to be seen if these prove to be superior.
- The new manufacturing technology of additive manufacturing (3D printing) does not appear to require special alloy compositions.
ACKNOWLEDGEMENTS
I would like to thank Massimo Poliero and his staff at Legor Srl for inviting me to present at the Jewellery Technology Forum once again. It is always a pleasure to present at this important international technology conference.
Thanks are also due to many friends and companies in the industry for information and allowing use of pictures and tables; these include Johnson Matthey, Legor,FEM, Progold, Platinum Guild International, Hoover and Strong and Techform.
REFERENCES
- D McDonald & L B Hunt, “A History of Platinum and its allied metals”, 1982, Johnson Matthey, Chapter 1. ISBN 0 905118 83 9
- E A Smith, “Working in Precious Metals”, 1933. Reprinted 1978, N.A.G. Press Ltd. Chapter 15. ISBN 7198 0032 3
- J S Forbes, “Hallmark – A history of the London Assay Office”, 1998, Unicorn Press/The Goldsmiths’ Company, Chapter 12. ISBN 0 906290 26 0
- G Ainsley, A A Bourne & R W E Rushforth, “Platinum Investment Casting Alloys”, Platinum Metals Review, 1978, vol 22(3), 78-87
- A A Bourne and A Knapton, US patent US4165983A, 1979/ UK patent GB58258A, 1981
- G Normandeau & D Euno, “Understanding Heat Treatable Platinum Alloys”, 1999, Santa Fe Symposium, ed D Schneller, Met-Chem Research Inc, 73-103. See also ibid,1998, Platinum Day symposium, Platinum Guild International, vol 5, 35-41
- J Huckle, “The Development of Platinum Alloys to overcome Production Problems”, 1996, Proc Santa Fe Symposium, ed D Schneller, Met-Chem Research Inc, 301-325. See also: J Huckle, “Choosing platinum alloys to maximise production efficiency”, Platinum Day symposium, 1995, Platinum Guild International, vol 1, 2-6,
- J Maerz, “Platinum Alloy Applications for Jewelry”, 1999, Proc. Santa Fe Symposium, ed D Schneller, Met-Chem Research Inc, 55-71 ,
- Maerz, “Platinum Alloys – Features and Benefits”,2004, Platinum Guild international. Download from the Ganoksin website: www.ganoksin.com/article/platinumalloys-features-benefits )
- E M Savitskii, “Handbook of Precious Metals”, English edition ed. A Prince, 1989, Hemisphere Publishing Corp., Chapter 6. ISBN0 89116 709 9
- P Battaini, “Metallography of Platinum and Platinum Alloys”, 2010, Proc. Santa Fe Symposium, ed E Bell, Met-Chem Research Inc, 27-49. Also: ibid, Platinum Metals Review, 2011, vol 55(2),74-83
- C W Corti, “Jewellery – Is it fit for Purpose?: An Analysis based on examination of customer complaints”, Presented at the Jewellery Technology Forum, Held at Vicenza, Italy, January 2018 (download from Legor/JTF website)
- C W Corti, “Jewelry – Is it fit for purpose? An analysis based on customer complaints”, 2018, Proc. Santa Fe Symposium, Ed E Bell, Met-Chem Research Inc, p163-175
- C W Corti, “Microalloying of High Carat Gold, Platinum and Silver”,, presented at the Jewellery Technology Forum, Vicenza, Italy, 17-18th June 2005. Publ. in conference proceedings.
- C W Corti, “Jewellery Alloys – Past, Present and Future”, Keynote lecture presented at the 1st Jewellery Materials Congress, Goldsmiths Hall, London, July 2019 (download from website https://www.assayofficelondon.co.uk/events/the-goldsmiths-company-jewellery-materials-congress .
- R W E Rushforth, “Machining Properties of Platinum”, Platinum Metals Review, 1978, vol 22 (1), p2-12
- C W Corti, “Basic Metallurgy of the Precious Metals – Part 1”, 2017, Proc Santa Fe Symposium, Ed E Bell, Met-Chem Research Inc, 25-61
- J C Wright, “Laser-welding platinum jewellery”, 2001, Proc Santa Fe Symposium, ed E bell, Met-Chem Research Inc, p455-468. See also J C Wright, “Jewellery-related properties of platinum”, Platinum Metals Review, 2002, vol 46(2) 66-72
- P J Horton, “Investment Powder Technology – The Present and the Future”, 2001, Proc Santa Fe Symposium, Ed. E Bell, Met-Chem Research Inc, 213-239
- J Maerz, “Platinum Casting Tree Design”, 2007, Proc Santa Fe Symposium, Ed E Bell, Met-Chem Research Inc, 305-322
- R Atkin, “Trouble Shooting Platinum Casting Defects and Difficulties”, 1996, Proc Santa Fe Symposium, Ed D Schneller, Met-Chem Research Inc, 327-337.
- P Lester, S Taylor & R Süss, “The Effect of different investment powders and flask temperatures on the casting of platinum alloys”, 2002, Proc Santa Fe Symposium, Ed E Bell, Met-Chem Research Inc, 321-334.
- U Klotz & T Drago, “The role of process parameters in Platinum Casting”, 2010, Proc Santa Fe Symposium, ed E Bell, Met-Chem research Inc, 287-325 and references therein. Also, ibid, Platinum Metals Review, 2011, vol 55(1), 20-27
- T Fryé & J Fischer-Buehner, “Platinum alloys in the 21st Century: A Comparative Study”, 2011, Proc Santa Fe Symposium, Ed E Bell, Met-Chem Research Inc, 210-229 and references therein. Also ibid, Platinum Metals Review, 2012, vol 56(3),155-171. An updated version also presented at the Jewellery Materials Congress, London, July 2019 (download from https://www.assayofficelondon.co.uk/events/the-goldsmiths-company-jewellery-materials-congress )
- K Weisner, “Heat treatable platinum for jewelry”, 1999, Platinum Day symposium, Platinum Guild International, vol 6, 25-30
- T Biggs, S Taylor & E van de Lingen, “The hardening of platinum alloys for potential jewellery application”, Platinum Metals Review, 2005, vol 49(1), 2-15.
- C W Corti, “Metallurgy of Microalloyed 24 carat Golds”, 1999, Proc Santa Fe Symposium, Ed E Bell, Met-Chem Research Inc, p379-402; also ibid, Gold Bulletin, vol 32(2), 39-47
- T Fryé, J T Strauss, J Fischer-Buehner, U Klotz, “The effects of Hot Isostatic Pressing of platinum alloy castings on mechanical properties and microstructure”, 2014, Proc. Santa Fe Symposium, Ed E Bell & J Haldeman, Met-Chem Research Inc, 189-209
- U Klotz, T Heiss, D Tilberto & F Held, “Platinum investment casting: Materials properties, casting simulation and optimum process parameters”, presented at Santa Fe Symposium, 2014 but published in Proc Santa Fe Symposium, 2015, ed E Bell et al, Met-Chem Research Inc, p143-180. Also, ibid, Johnson Matthey Technology Review, 2015, vol 59(2), 95-108 & 129-138
- T Fryé & U Klotz, “Mechanical properties and wear resistance of platinum jewelry casting alloys: A comparative study”, 2018, Proc Santa Fe Symposium, ed E Bell et al, Met-Chem Research Inc, 235-273.
- T Laag & H-G Schenzel, C Hafner GmbH, German patent application DE10212007299A1, 17.10.2013,
- U Klotz & T Fryé, “Mechanical properties of platinum jewellery casting alloys”, 2019, Johnson Matthey Technology Review, vol 63(2), 89-99
- J Maerz & T Laag, “Platinum Alloys, Features and benefits: comparing six platinum alloys”, 2016, Proc Santa Fe Symposium, ed E Bell et al, Met-Chem Research Inc, 335-353
- R Lanam, F Pozarnik, T Volpe, “Platinum alloy characteristics: A comparison of existing platinum casting alloys with Pt-Cu-Co”, 1997, Platinum Day symposium, Platinum Guild International, vol 3, 2-12
- G Normandeau & D Ueno,”Platinum alloy design for the investment casting process”, 2000, Platinum Day symposium, Platinum Guild International,, vol 8, 41-49
- S Grice & C Cart, “PlatOro™: The perfect marriage”, 2002, Platinum Day symposium, Platinum Guild International, vol 10, 4-7
- S Grice, Private communication, June 2021
- R Bertoncello & J Fischer-Bühner, Legor patent application ITM120110750A1, 2011 “Platinum-cobalt alloys with improved hardness”.
- T Trosch, F Lalire, S Pommier, R Völkl, U Glatzel, “Optimisation of a jewellery platinum alloy for precision casting: Evaluation of mechanical, microstructural and optical properties”, 2018, Johnson Matthey Technology Review, vol 62(4),364-382.
- U Klotz, D Tilberto & F Held, “Additive manufacturing of 18 karat yellow gold alloys”, 2016, Proc Santa Fe Symposium, ed. E Bell et al, Met-Chem Research Inc, 255-272
- D Zito, A Carlotto, P Sbornicchia et al, “Optimisation of SLM technology main parameters in the prodiction of gold and platinum jewellery”, 2014, Proc Santa Fe Symposium, ed E bell & J Haldeman, Met-Chem Research Inc, 439-469
- D Zito, V Allodi,, P Sbornicchia & S Rappo, “Why should we direct 3D print jewelry? A comparison between two thoughts: Today and tomorrow”, 2017, Proc Santa Fe Symposium, ed E Bell et al, Met-Chem Research Inc, 515-556
- D Zito, A Carlotto, A Loggi, P Sbornicchia, D Bruttomesso & S Rappo, “Definition and solidity of gold and platinum jewlry produced using selective laser melting (SLM™) technology, 2015, Proc Santa Fe Symposium, ed E Bell et al, Met-Chem Research Inc, 455-491
- D Zito, “Potential and innovation of the selective laser melting technique in platinum jewelry”, 2018, Proc Santa Fe Symposium, ed E Bell et al, Met-Chem Research Inc, 625-684
- G Steiner, “Platinum Alloy for Jewelry”, European patents EP 2260116B1, 2014 and EP 209994181, 2007, Heimerle & Meule GmbH,
- E Leoni et al, “Platinum alloy” European Patent EP3502286 (A1), 2019, Omega SA.
Note: Papers published in Platinum Metals Review/Johnson Matthey Technology Review can be downloaded free from the archive at https://www.technology.matthey.com/ . Many papers from the various Santa Fe Symposia can be downloaded free from the Santa Fe Symposium website archive at www.santafesymposium.org . Papers from Gold Bulletin can be downloaded from the Springer/Gold Bulletin website at https://link.springer.com/journal/13404/volumes-and-issues