Nickel Release from 316L Stainless Steel Following a Ni-Free Electroplating Cycle: Mechanisms and Surface Treatment Influence
Roberta Emanuele
316L stainless steel (SS) is generally regarded as safe due to its high corrosion resistance and passivation properties, which inhibit metal release. However, this study demonstrates that electroplating can induce significant nickel release, even from 316L SS, challenging the assumption of its inertness. Nickel release was evaluated following a Ni-free electroplating cycle, and the findings were measured according to the EN 1811 standard for nickel release. The research investigated the effect of surface treatments and electroplating techniques on nickel release, focusing on the role of surface roughness and internal stresses. Comparisons were made between polished and unpolished 316L SS samples, revealing that smoother surfaces tend to exhibit less nickel release. Moreover, the study showed that increased thickness of the electroplated precious metal layer can mitigate nickel release, while internal stresses generated during the electroplating process can exacerbate it. Additionally, coatings obtained through physical vapor deposition (PVD), which preserve the passivation layer of the steel, did not exhibit any nickel release. These findings suggest that the primary cause of nickel release stems from the removal of the stainless steel’s passivation layer and the microporosity introduced during the electroplating process. This combination weakens the protective chromium oxide film, allowing nickel to leach from the alloy.
In conclusion, nickel release from 316L SS can be minimized by optimizing surface treatments and maintaining the integrity of the passivation layer, particularly when employing electroplating techniques for applications where nickel exposure must be strictly controlled.
Bio
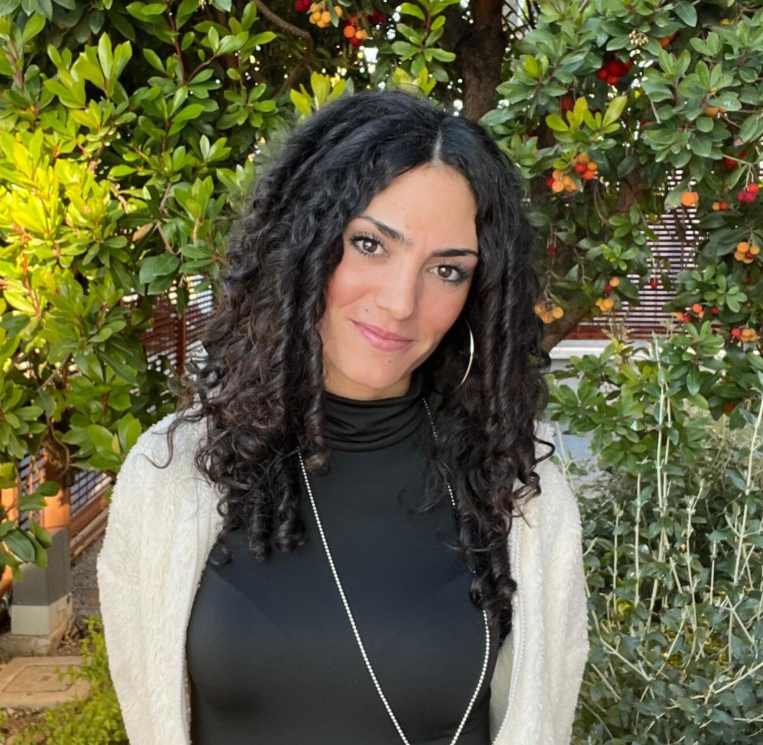